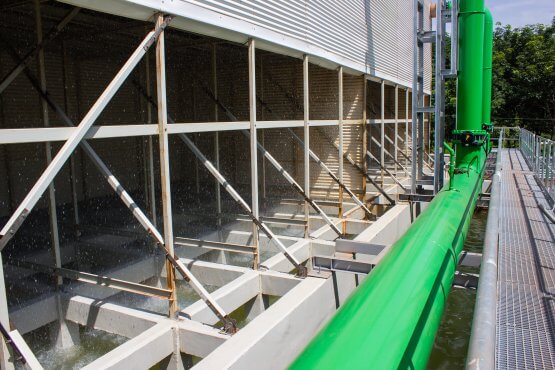
A Regional Laboratory for a leading environmental agency in Houston, Texas was having problems with dirty cooling tower water. The dirty water lead to HVAC loop system downtime, increased labor, and maintenance costs. The agency acted fast to find a solution for their dirty cooling water problem as well as set an example of water and energy conservation. To meet the agencies needs, they installed a LAKOS TCX-0280-SRV and were able to filter out sand, silt, scale, and rust from their cooling tower water with a zero liquid loss approach to filtration. The solution also reduced maintenance and downtime costs while improving thermal efficiency in downstream equipment. Learn More
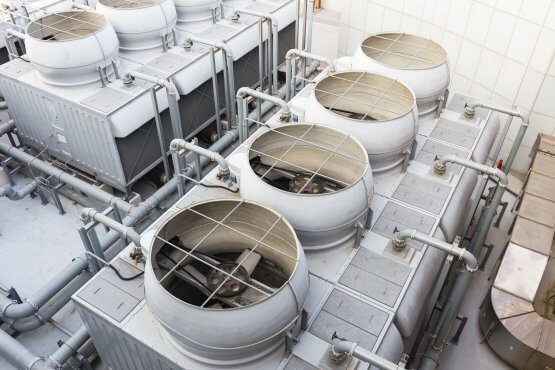
At National Wire Products Corporation in Baltimore, Maryland it was a big job to keep their ejector-type cooling towers in operation. Normally, they would need to clean the system at least once a week, but once they installed in three LAKOS In-Line Separators, they do the cleaning themselves. The LAKOS separators now reduce cooling tower problems by about 95%, allowing for a reduction in downtime and maintenance costs. Learn More
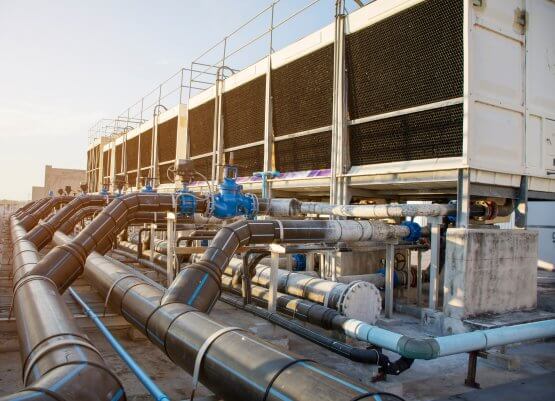
A General Electric plant in Cleveland, Ohio producing tungsten wire and powder constantly suffered from contaminated, dirty cooling water. Their cooling water was contaminated with airborne grit and would accumulate in their large cooling tower, which required constant maintenance and inspection at least once every shift. General Electric began looking for a more efficient way of keeping their water and cooling towers free of grit. General Electric first installed a side-stream LAKOS Separator and then added two Industrial Model Separators. In no time, the LAKOS Separators were paying for themselves, removing up to 98% of all solids and reduced cleaning cycles to every six weeks. Learn More